ABOUT US
eXtended Particle Simulations
XPS (eXtended Particle Simulations) is a highly efficient CFD-DEM simulation software, which is able to predict in detail fluid-granular processes.
It enables the user to understand, control and predict pharmaceutical unit operations leading to enhanced efficiency and improved product quality. XPS uses the Discrete Element Method (DEM) and advanced contact models to describe the bulk behavior with unmatched accuracy.
Massively parallel algorithms natively developed for modern Graphics Processing Units (GPUs) ensure the fastest execution times – even on desktop machines. Understanding failures, optimizing processes, and designing control strategies become feasible.
PARTNERSHIP
RCPE-IST Cooperation
The Research Center Pharmaceutical Engineering (RCPE) and InSilicoTrials (IST) have agreed to an exclusive partnership to commercialize the XPS simulation software. Specifically developed for pharmaceutical applications, XPS allows companies to assess their process configurations in unprecedented detail and explore the decision space without time- and labor-intensive experiments. While RCPE is responsible for the development, IST handles the software solutions worldwide distribution and first-level support
SERVICES
What do we offer?
XPS Software package (DEM/DEM-CFD/Cloud)
Training
Technical support
Consulting engineering
Cloud
BENEFITS
What makes XPS
stand out?
XPS is more than a software: the experienced engineering and development team support our customers, offering customized solutions and ensuring maximum software usability.
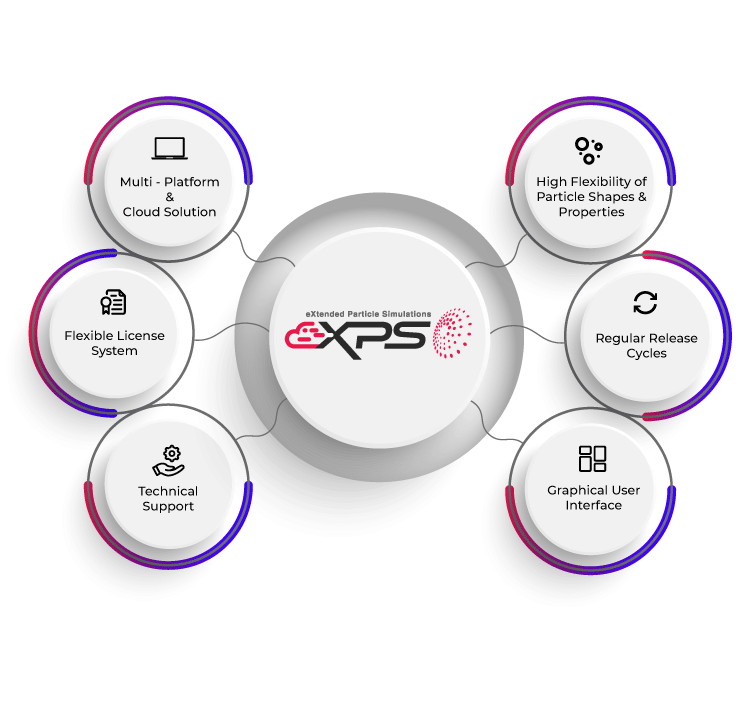
INDUSTRIES
Who do we target?
Prediction and understanding of fluid-granular flow is necessary for many industries
Pharmaceutical
University & Academia
Food Processing
Equipment Manufacturer
APPLICATIONS
Understand, Predict and Control.
It is estimated that more than 70% of products in industry are manufactured as particulate solids. Being able to understand, control and predict these granular flows is required in a wide range of unit operations in the pharmaceutical, chemical, food or agriculture industry. Besides many more, typical applications include:
Die filling
Drying
Feeding
Blending and Segregation Analysis
Dry and wet granulation
Screw and pneumatic conveyors
Hot-melt extrusion
Fluidized beds
Key Benefits
Intuitive and easy-to-use graphical user interface for quick simulation set-up
Simulation of large and complex particle systems at unparalleled computational speed – at-least five times faster than other commercial solutions
Capable of handling up to 100 million particles on a single GPU*
High flexibility in terms of particle shapes, sizes and properties
Modeling of cohesive powder flows thanks to the integration of advanced contact models
Coupling with CFD (computational fluid dynamics)
Physics models validated for pharmaceutical applications
Software development practices ISO validated: ISO 90003:2018 Software Quality Management and ISO 9001:2015 Quality Management
Cloud solution within XPS portfolio
SimTabletCoater
RCPE and InsilicoTrials have joined forces to facilitate tablet coating simulations via an easy-to-use cloud interface. The GPU-based DEM solver XPS, developed by RCPE, is integrated into the InSilicoTrials web platform, adding an additional tool to the comprehensive model portfolio: SimTabletCoater.
SimTabletCoater assists process engineers in selecting ideal operating conditions for process establishment and scale-up so you can shorten your product development cycles and significantly reduce the time to market. Simple inputs, standardized post-processing, automated reporting, and unmatched parallel speed make it possible to make informed decisions about critical process settings, such as the spray rate, the rotational speed, or even the coater design.
Get your tablet coating process right the first time and contact InSilicoTrials to start using SimTabletCoater!
USE CASES
XPS Use Cases
Tablet Coating
Tablet coating is a common unit operation in the pharmaceutical industry. It is of particular importance since it usually marks the last manufacturing step before the tablets are packaged and made available to patients. XPS enables the process simulation including various tablet shapes and complex device geometries. In addition XPS holds a variety of physical models in order to predict, e.g., spray drying and coating distribution based on the nozzle characteristics. The typical output of these analysis include the coefficient of variations (CoV), spray losses and cycle time and force distributions which can be related to chipping and twinning.
Blending
Blending is a widely-used process during the production of solid oral dosage forms. But especially for cohesive powders, achieving a homogeneous blend can turn into a delicate task with little degrees to freedom to operate on. XPS helps to understand the behavior of granular materials in the mixing process. Among others, charging scenarios can be optimized and the influence of batch mass and operating conditions on the blend homogeneity can be studied. This leads more economic processes including a reduced risk of over-blending.
Fluidized Bed
Fluidized beds are used for spray-drying or mixing. Since several phases are involved (i.e. granular matter, gas, fluid), this processes tend to be challenging. Using a hybrid CPD-GPU CFD-DEM approach, XPS can be coupled with the CFD solver AVL FIRETM. The two-way coupling offers a wide variety of analysis options, e.g. coating, mixing, temperature.
TECHNICAL DETAILS
Architecture Specifications
- Optimized to drastically reduce the computational demand per time-step and the memory consumption
- No need for a professional equipment: it works with an ordinary workstation (up to 4 GPUs, one simulation per GPU)
- Multiple platforms supported (MS Windows, Linux, Cloud)
- Native CUDA code (Nvidia GPU required)
- DEM/CFD coupling: reduced transferred data amount between the DEM and the CFD codes, which depends only on the number of the DEM cells and not on the number of particles
- The two codes run on separated computing platforms (CPUs and GPUs): the computing performance of each code is not affected by the other
Lorem ipsum dolor sit amet
Features and Modules
- Fully developed Graphical User Interface (GUI)
- Handling of complex geometries (STL)
- Handling of many millions of particles
- DEM – CFD coupling to model complex multi-physics phenomena
- Clumps (Multi-spheres), Tablets
- Heat exchange
- Spray modeling (coating, impregnation)
- Post-Processing tools and support for analyzing simulation results
XPS RELATED PUBLICATIONS
Large-scale CFD–DEM simulations of fluidized granular systems, Chemical Engineering Science, Volume 98, 2013, Pages 298-310.
D. Jajcevic, E. Siegmann, C. Radeke, J. G. Khinast
Simulation of a tablet coating process at different scales using DEM, European Journal of Pharmaceutical Sciences, Volume 93, 2016, Pages 74-83
P. Boehling, G. Toschkoff, S. Just, K. Knop, P. Kleinebudde, A. Funke, H. Rehbaum, P. Rajniak, J.G. Khinast
Detailed modeling and process design of an advanced continuous powder Mixer, International Journal of Pharmaceutics, Volume 552, Issues 1–2, 2018, Pages 288-300.
P. Toson, E. Siegmann, M. Trogrlic, H. Kureck, J. G. Khinast, D. Jajcevic, P. Doshi, D. Blackwood, A. Bonnassieux, P. D. Daugherity, M. T.
Extended validation and verification of XPS/AVL-Fire™, a computational CFD-DEM software platform, Powder Technology, Volume 361, 2020, Pages 880-893.
T. Forgber, P. Toson, S. Madlmeir, H. Kureck, J. G. Khinast, D. Jajcevic